Diamond Paints Optimizes Supply Chain Using LMKT’s WFM SolutionWorkforce Management
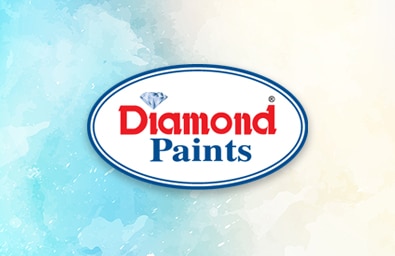
LMKT’s workforce management solution, WFM, enabled Diamond Paints to monitor sales activities in real time, collect accurate data on potential customers and track idle time of its field staff.
0
Nationwide Sites Surveyed
0
Total Teams
0
Data Collection Automation
0
Staff Idle Time Reduction
0
Potential Customers Identified
Challenge
To manage its supply chain for its dealers, Diamond Paints was facing two main problems. The dealers were located across the country, making tracking of sales personnel in the field a problem. Also there was no accurate record of attendance for the field staff and no path to verify the visits they made to different sites.
The second problem that Diamond Paints faced involved data collection. The data was collected manually on paper and as a result was prone to delays and mistakes. After the initial collection the business faced problems in the verification of the collected data and the filing of paperwork.
This cumbersome process resulted in delayed responses to potential customers. This not only resulted in loss of business for the company but also caused low level of satisfaction among the company’s customers.
As a result, Diamond Paints needed a solution that not only made the overall process simpler and efficient but also more auditable.
Solution
Implementation of WFM, LMKT’s workforce management solution for the field staff, provided Diamond Paints with the ability to accurately track the location of its field force. Diamond Paints has a team of around 400 individuals and a network of several outlets. The deployment also gave supervisors the ability to monitor the activities of their field teams in real time throughout the day. Through a global map overview that provided the assignment status of every field worker, WFM enabled managers to keep the track of their teams overall performance on a day to day basis.
WFM mobile application enabled staff to mark their daily attendance and collect data using their mobile phones. Real time syncing of the data, collected though field forms by the staff, ensured the verification of customer data. To safeguard data in case the battery of a mobile phone runs out, WFM monitors the battery time with each submission completed by field staff and executes periodic sync of battery life each time the battery drops 5%. In case of a bad network, field staff has the option to store data in offline mode and then sync the data online when there is a better network connection available.
Benefits
WFM serves as an effective solution for Diamond Paints due to the tools it provides for speedy collection of accurate data collected and for enhanced staff management.
Monitoring and Control
LMKT’s WFM solution has assisted Diamond Paints in saving staff time both in the field and in the office. By tracking the attendance and idle time of the workers in real-time, the system allows supervisor to better manage their teams and identify any bottlenecks in the workflow.
GPS Logging
Automatic GPS logging of records eliminated the risk of incorrect recording of location as well as the risks associated with transcribing and transcoding of information. This has also made the data collection simpler. The photo-capturing feature, which allows the field staff to take photos and link it to the respective site after their visit has further reduced the risk of an error.
Offline Data Collection
Diamond Paints is benefitting from WFM’s capability to perform data collection offline and then periodically sync this data to a central server. Wi-Fi and cellular are not available all the time in remote areas of Pakistan. Through this offline data collection feature, field staff does not have to rely on an active mobile connection for data collection.